Evolution of Steel Piling Walls for Post Panamax Marine Structures
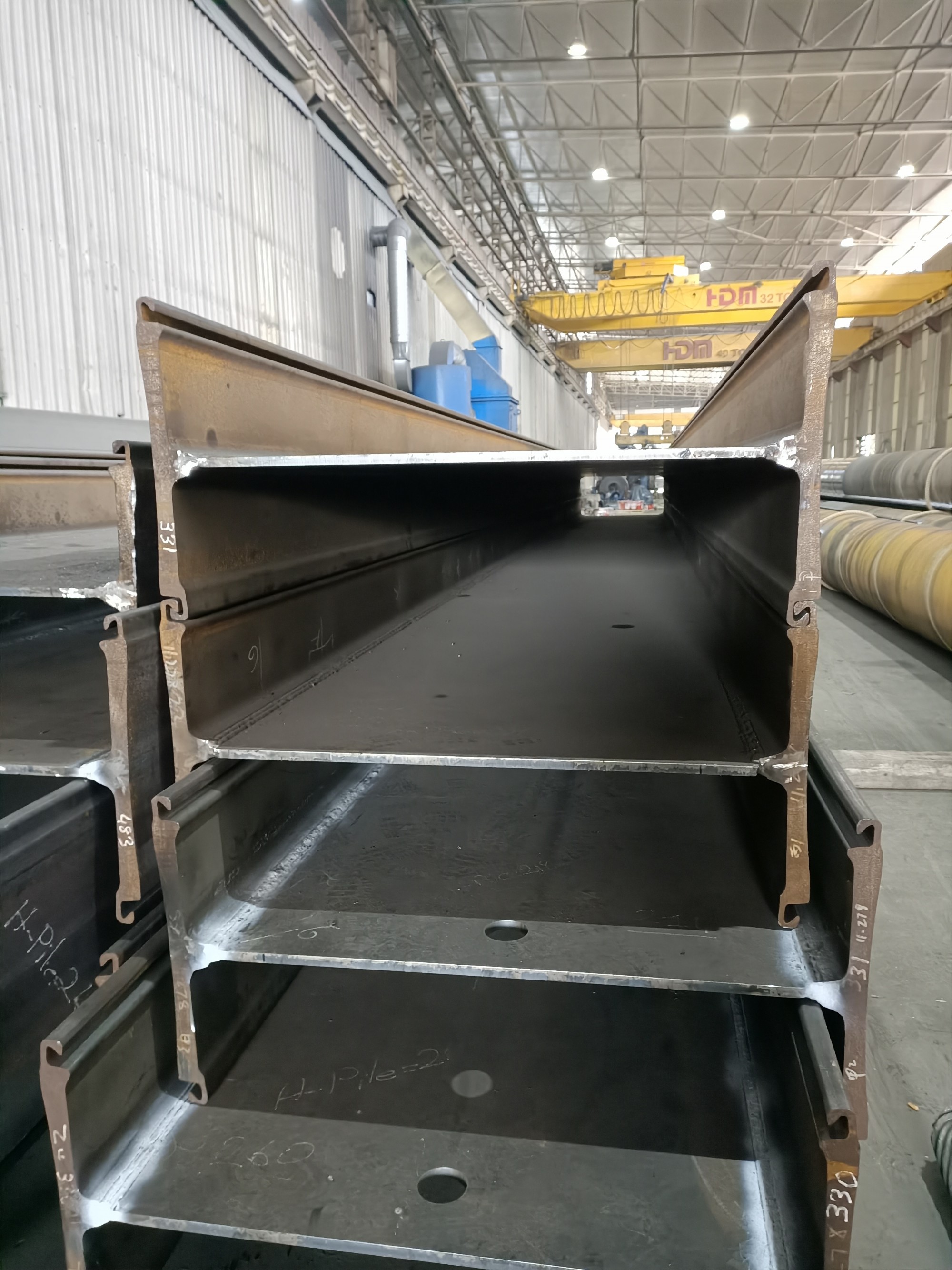
Sheet Piling, B.C. (Before Combi-walls)
Prior to the inception of combined wall systems, sheet piles were commonly used for earth retention and support of excavation projects. At this time, the largest domestic sheet pile available had a section modulus of ~60 in³/ft. If design stresses exceeded that, engineers had to get creative by adding steel cover plating to the top and bottom flanges of the pile.
The additional steel would boost the section properties. This cover plating fabrication was a solution for a time when heavy civil/marine applications like deep excavations and port berthing structures needed higher moduli than sheet pile could offer. It was effective, but not the most efficient solution. The plating material and fabrication were costly with poor engineering economics.
Today, there are at least two hot rolled sheet pile series with wider, lighter, stronger sections that approach moduli of 100 in³/ft. Now, cover plated applications are rare and considered a last resort only when efficient heavier sections are not available.
The Right Combination
Higher modulus wall solutions were explored early on by steel pile manufacturers. Dating back to the early 1900’s, mill engineers envisioned multiple concepts but as with most innovations, barriers to market like manufacturing costs, application demand and expected return on investment dead-ended most patent applications before they received serious market and production consideration.
The real breakthrough in high modulus wall design came when pile producers realized that combining existing steel sheet pile sections with large beam shapes, (King Pile Combi-Wall) resulted in high modulus system properties and weight efficiencies like no other prior concept.
The marriage of two conventional hot rolled sections made the combi-wall concept more attractive to producers with lower financial risk to develop. Unlike Wide Flange (WF) beams, H-King pile beams are designed to be geo-structurally supported, so the buckling and slenderness ratios that govern unsupported column design can be stretched, allowing for deeper, wider and lighter sections compared to standard wide flange shapes.
There are two domestic mills that currently make hot rolled sheet piles, but neither produce an H King pile. Suppliers can offer an alternate king pile system with domestic sheets and WF beams, but they have engineering and material limitations. Only one North American beam producer makes the heavier, deeper WF sections to compete. Even still, the flange widths are narrow, and the weld-on connector locations reduce properties. The result is heavier unit weights with lesser strength. Lastly, the weld on connectors are rarely domestically produced. For these reasons, 100% domestic King beam systems are less viable and not optimal.
Combi-Wall Breakdown
Traditional high modulus combined walls are made up of three components: 1) King pile – the primary load member, either beam or pipe. 2) Sheet piles – the intermediate spanning elements that reduce panel weight but contribute very little structurally. 3) Interlocking clutch bars - the weld-on connectors that structurally join the two piles. The system width is measured in panels from the centerline of one king pile, across the sheet piles to the centerline of the other. Like sheet pile, combi-wall properties are specified in the same units; section modulus (in³/ft), moment of inertia (in⁴/ft) and bending moment (kip-ft/ft). When a designer or contractor is considering pipe or H-beam combi-wall options; wider, lighter, and stronger are usually the key measurables, but there are commercial, structural and installation factors that impact overall cost and feasibility.
Pipe Z & H-King Z: Pros & Cons
The shape of the primary load member (beam or pipe) has pros and cons. Pipe can get wide and deep, so the inertial properties are very good, but the cross sectional area is spread throughout the diameter so the section modulus is not proportionate and often lower than what the analysis requires. More steel is needed, so the pipe wall thickness must increase. Striking a balance between the diameter (30” – 84”) and wall thickness (0.375” – 1.0”) to achieve both modulus and inertia properties can be an iterative process. The pipe Z panel widths (7.5’ – 12’) are wider and require less panels to install compared to H-King single and double beam configurations (5.75’ – 8.33’), but the pipe Z unit weight is typically higher and site restrictions may limit the O.D. Also, a larger OD pipe will likely present more difficult driving challenges, have more concrete and rebar for the splash apron, cap and moment connection compared to an H King pile set up. Pipe may also have backfilling requirements inside the pile. On the plus side, pipe is readily available with ample domestic and foreign production. Hot rolled Z sheets also have foreign and domestic options and the weld on pile connectors are well sourced. If the material is available, 10 – 12 week lead times are possible. These are all factors that should be considered when evaluating a high modulus wall solution.
H-King High Modulus Wall Market
H-King beams like the HZM are specifically designed for high modulus wall loading to maximize structural properties and weight efficiency. They achieve very high numbers with single and double pile layouts using 33”- 48” deep beams, but no domestic mills produce a true H King system, so lead times typically range from 14-18 weeks. All these factors should be considered when evaluating the most economical solution. Salzgitter Mannesmann’s Peiner Hoesch system (Germany) was the only formidable competitor until the line was discontinued in 2016. The current ArcelorMittal HZM system is an evolution from the original Arbed HZ predecessor. Beam modifications and mill upgrades in the mid 2,000’s, combined with 700mm & 770mm AZ sheet piles resulted in better strength to weight efficiencies, further distancing their competitive advantage. Since then, HZM has been the sole sourced King beam combi-wall system throughout the world.
Traditional King Beam and Pipe combi-wall systems all share a common thread in their build and functionality, that is welded interlock connectors. These components add 20-45 plf of weight depending on single or double configuration and require costly weld fabrication. Imagine the time and money to be saved eliminating all that. That is exactly what Fields set out to do in 2017 when they developed the new HMZZ system. Not interested in just another “me too” king beam system, Fields developed an innovative concept to produce a beam system that not only eliminated the welded interlock connection, they were able to break through the system limitations of traditional steel beam rolling process.
After multiple design iterations, the breakthrough came in the shape of a unique hot rolled flange with an integrated hot rolled Larssen interlock and a drop nose web connection.
The nose shape serves 3 structural purposes;
- it pushes the web-flange connection away from the x-y plane, addressing any concerns having the weld in the shear axis.
- it gives the beam strength to resist transverse stresses in the same manner as hot-rolled beams or the flange-web transitions in a hot-rolled sheet pile.
- it provides an excellent surface area for automated full penetration welds.
In addition, the Direct Connect flange rolling technology allows JD Fields to build the web height, thickness, and bottom flange to a customer’s specific application requirements. These customizations result in maximum system strength with weight efficiency while eliminating the welded interlock connection.
Features & Benefits
From a commercial perspective, removing 2, 4 or 6 clutch connectors can reduce system weight up to 40 lb/ft per beam while decreasing fabrication costs and lead time. Regarding drivability, high modulus beam lengths can exceed 100’ with driving depths of 60’ or more. H King beam shapes have the best section characteristics to meet those challenging driving conditions. If there is a weak link to traditional combined wall systems, it is the welded clutch connection. In comparison, the HMZZ beam - sheet interlock connection is an integral part of the beam flange, not a component add-on.
Also, the single-beam configuration does not require a bottom interlock connection, so further material savings are realized by using hot rolled plate.
In a double king pile (DHZZ) scenario, the direct connect flanges are needed on top and bottom to interlock the beams, but the system flexibility allows for two flange thicknesses. Both HZF 40 & HZF 30 flanges are available for design consideration. These product innovations set HMZZ’s engineered beam technology apart from any other.
Paradigm Shift
Combined walls are marketed and specified through lookup tables in product catalogs. The current industry-standard system is comprised of 11 beams varying in weight and height, with 2, 4 or 6 connectors, and 3 typical stock sheet pile sections. These components are offered in a variety of single and double beam configurations resulting in over 100 wall solutions. The HMZZ Direct Connect system is not limited to a finite number of beams or connectors. The hot rolled flange design and fabrication process allows for unlimited combinations of beam height, web, and flange combinations for single and double beam layouts. This is the first and only high modulus combi-wall system that can design and build a custom wall solution based on the specific application requirements. This is a complete one-eighty for the catalog specification process that challenges conventional print marketing.
The Wallbuilder online platform is currently under construction, but Fields is already quoting and taking orders. The HMZZ Wallbuilder Calculator tool and Wallbuilder Software Platform are comprehensive design and commercial marketing tools with cradle to grave functionality. From geo-structural analysis, durability and cost engineering, to custom generated CAD files and data sheets, this virtual platform will revolutionize high modulus wall applications.
Owners, engineers and contractors working in the marine piling and deep foundation industry have a lot to be excited about. Look for the Wallbuilder platform to launch after the New Year. If you would like to learn more, Fields’ offers no cost engineering seminars and lunch & learns on the HMZZ system and its Wallbuilder design software.
MORE POSTS
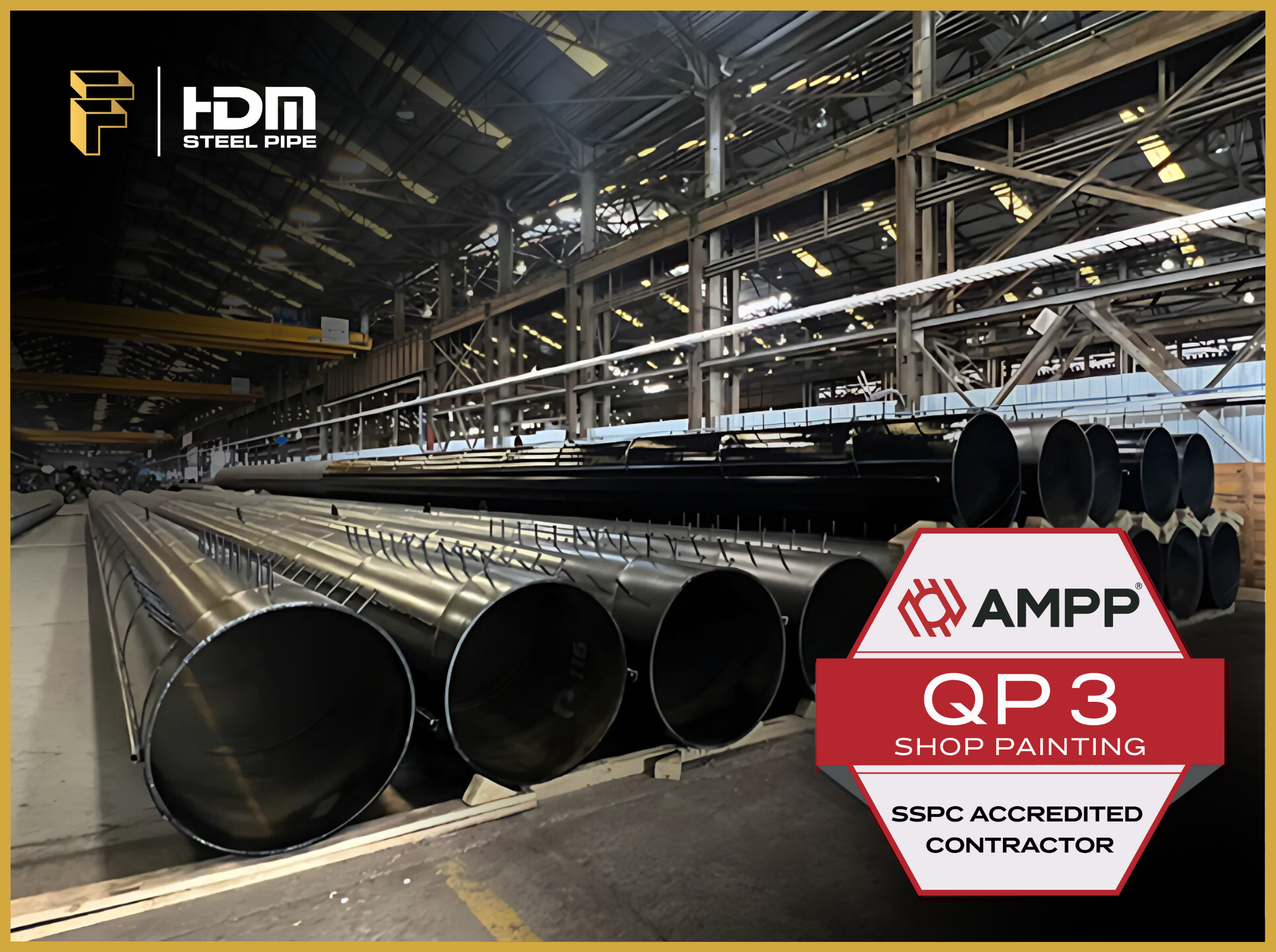
JDF-HDM Spiralweld Pipe Mill has been awarded QP3 Certification by AMPP
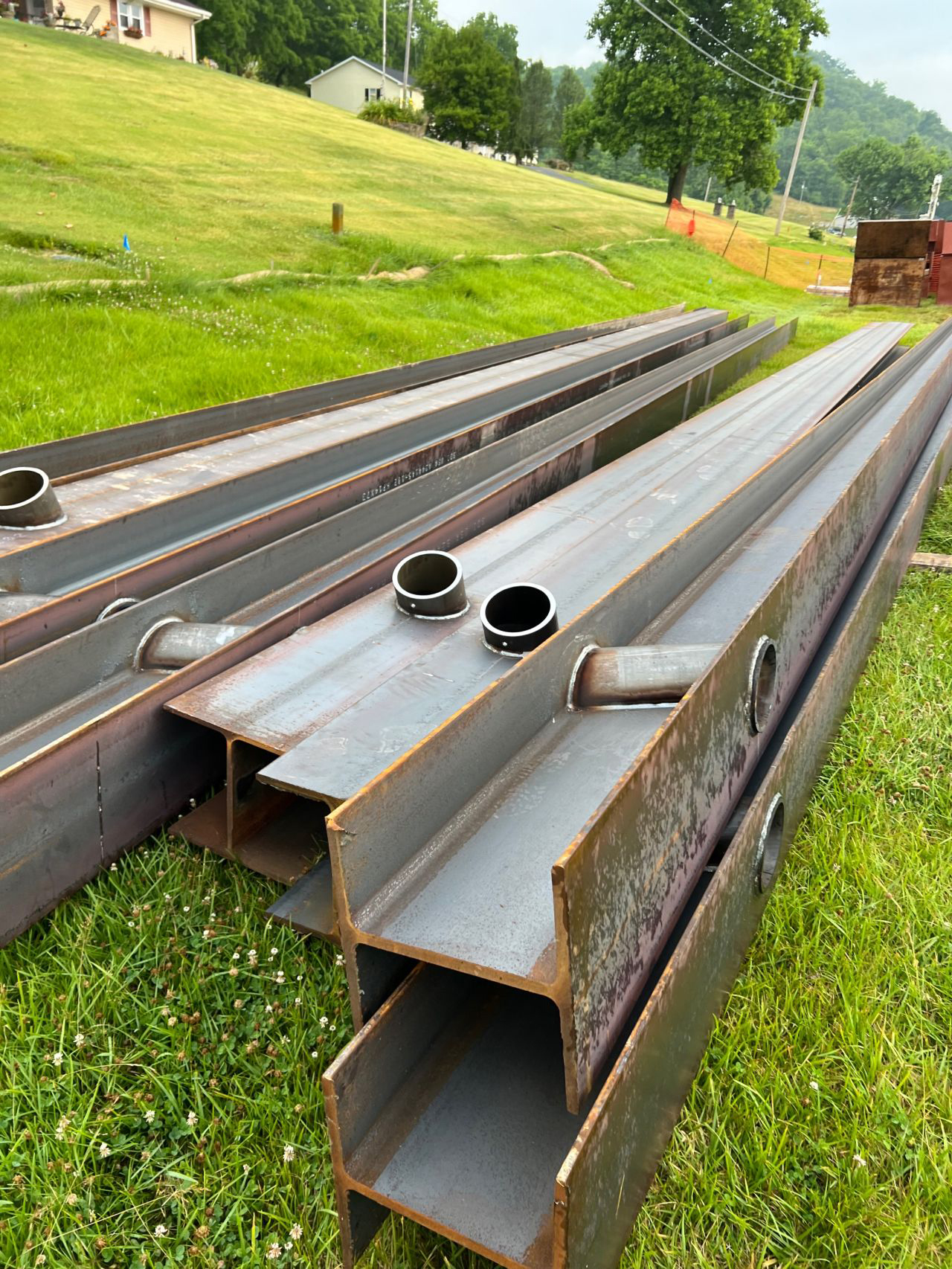
SR-156 Slide Repair - Switzerland County, Indiana
%20(1)_small.jpg)
McCoys Creek Restoration - Jacksonville, Florida
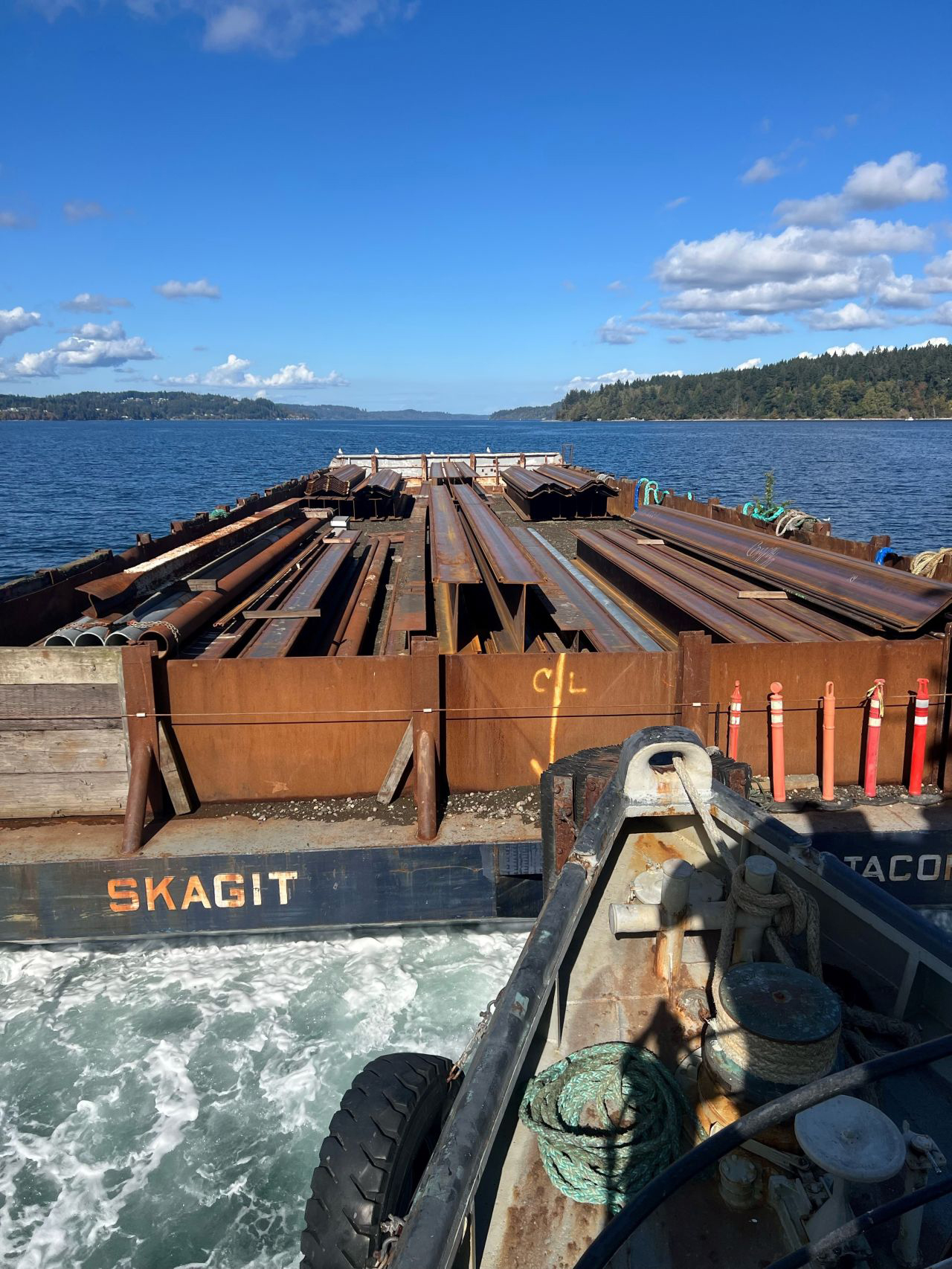
Port of Bellingham Terminals I & J Waterway Cleanup Action - Washington
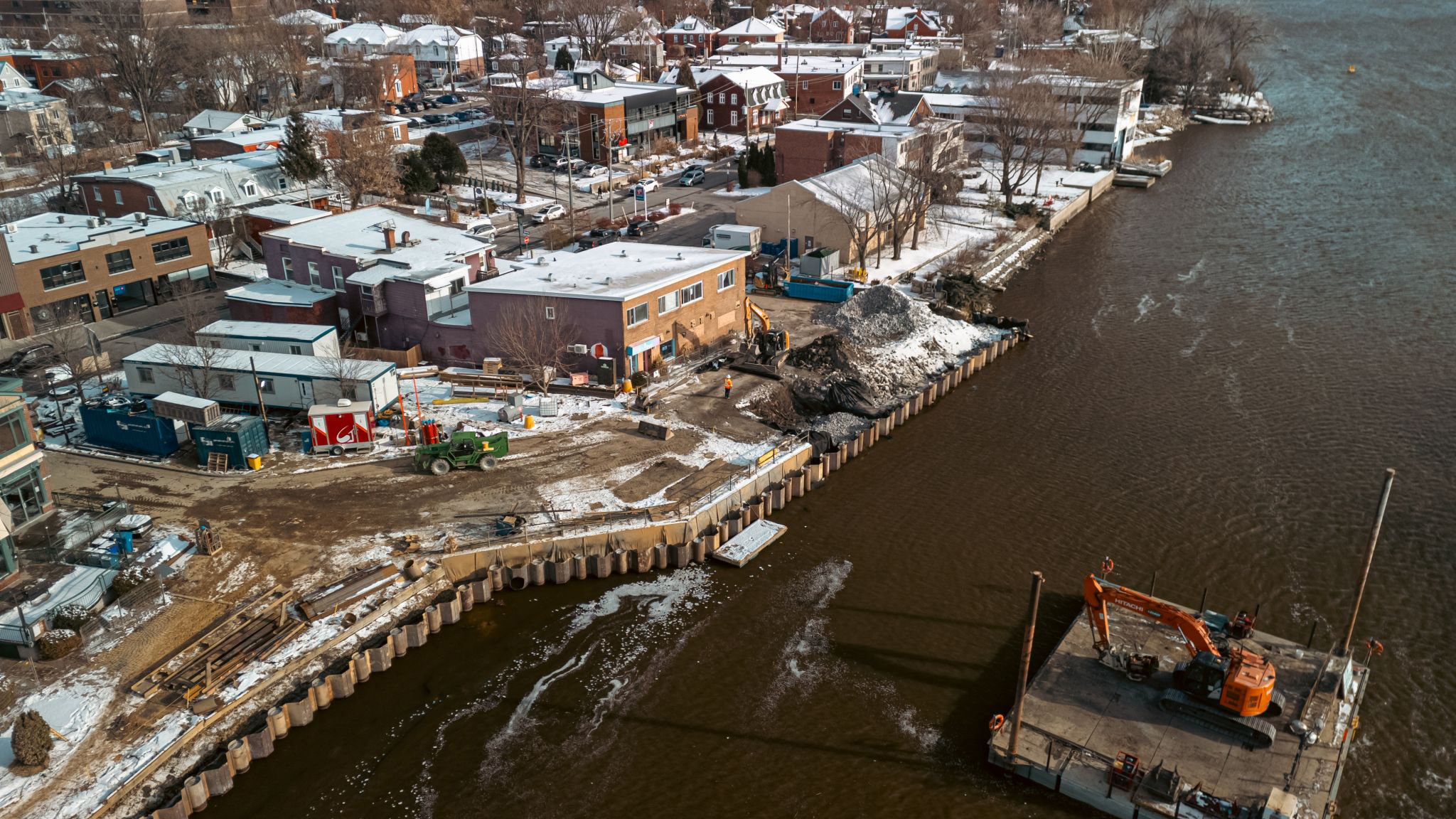
Pipe Z Combi-Wall Solution - Ste-Anne-de-Bellevue, QC
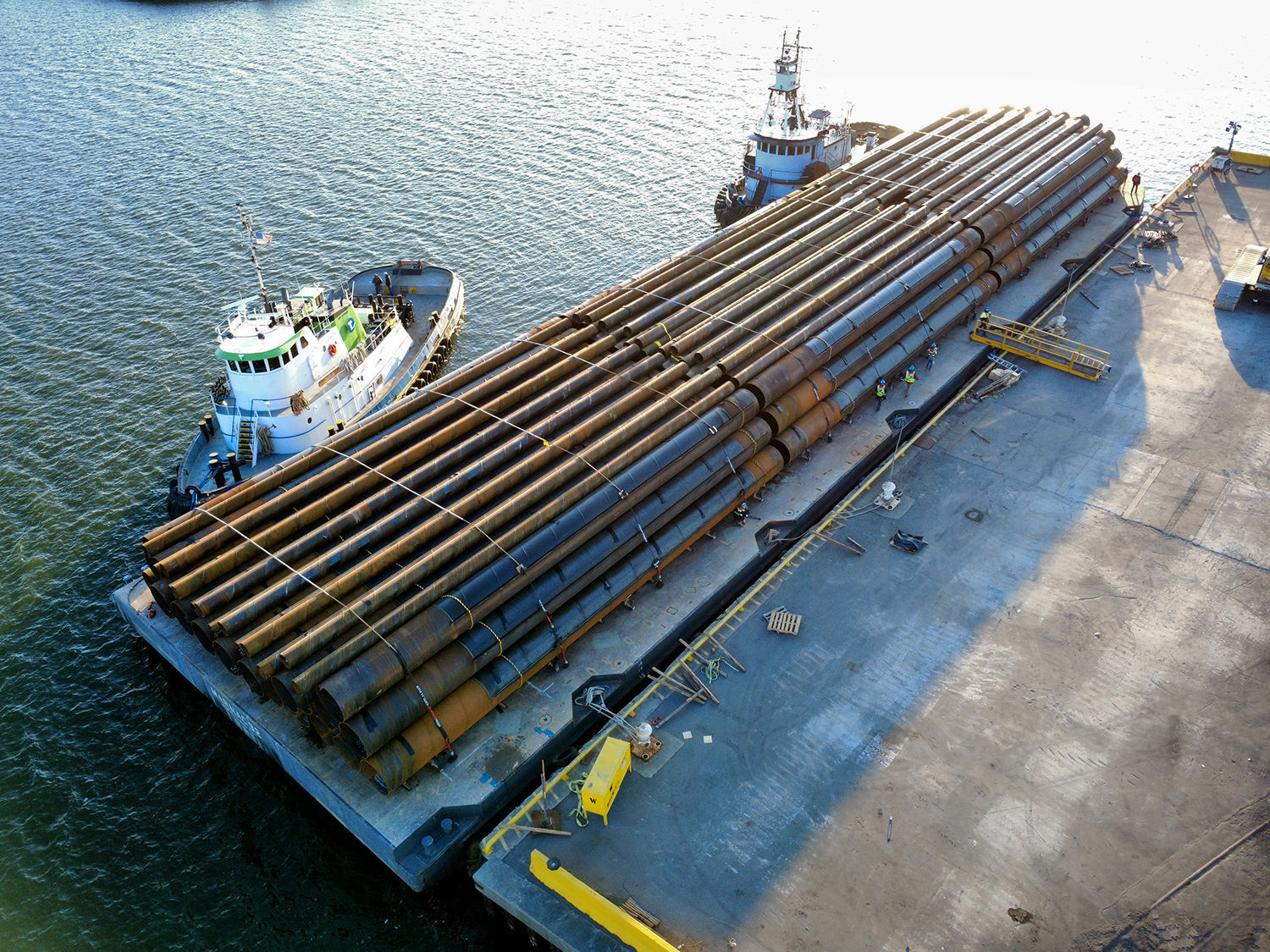
PZC Sheet Piles & Spiralweld Pipe - Port of Tampa Bay
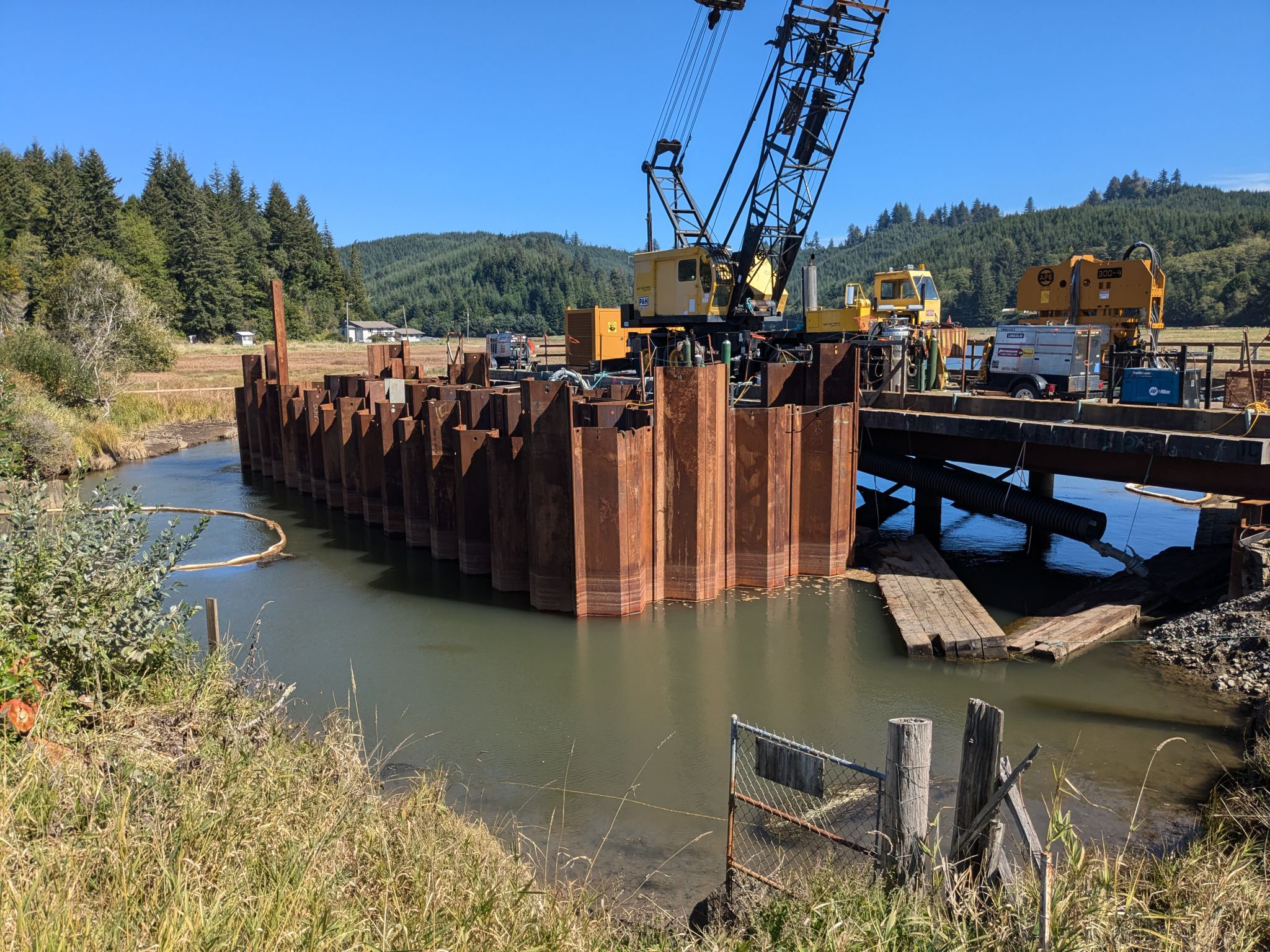
Tide Gate Structure - North Bend Oregon
.png)
Celebrating 40 Years of JD Fields: A Legacy of Excellence and Innovation
.jpg)
The Evolution of High-Frequency Welded Line Pipe
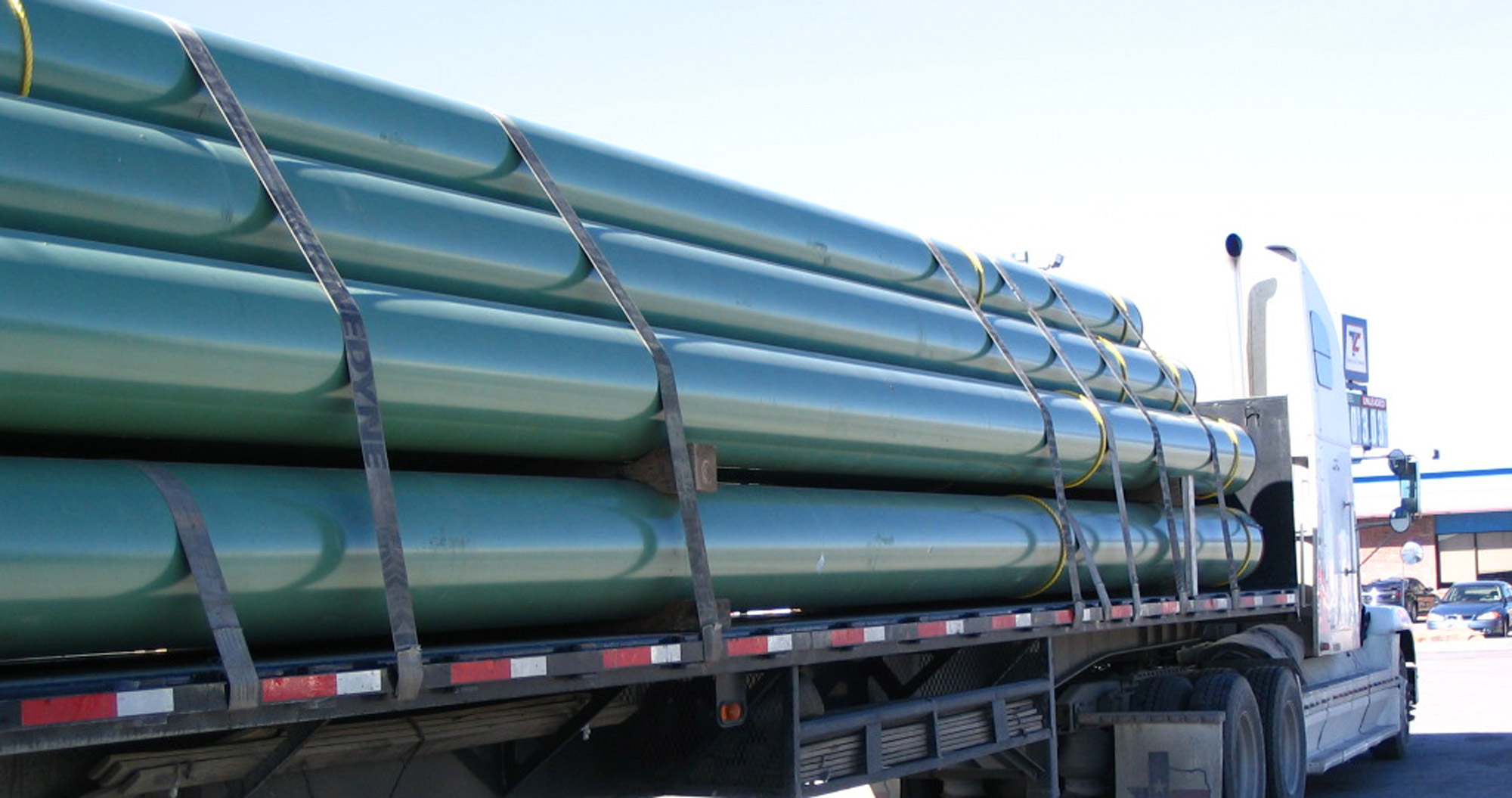
The Amazing Properties of Steel
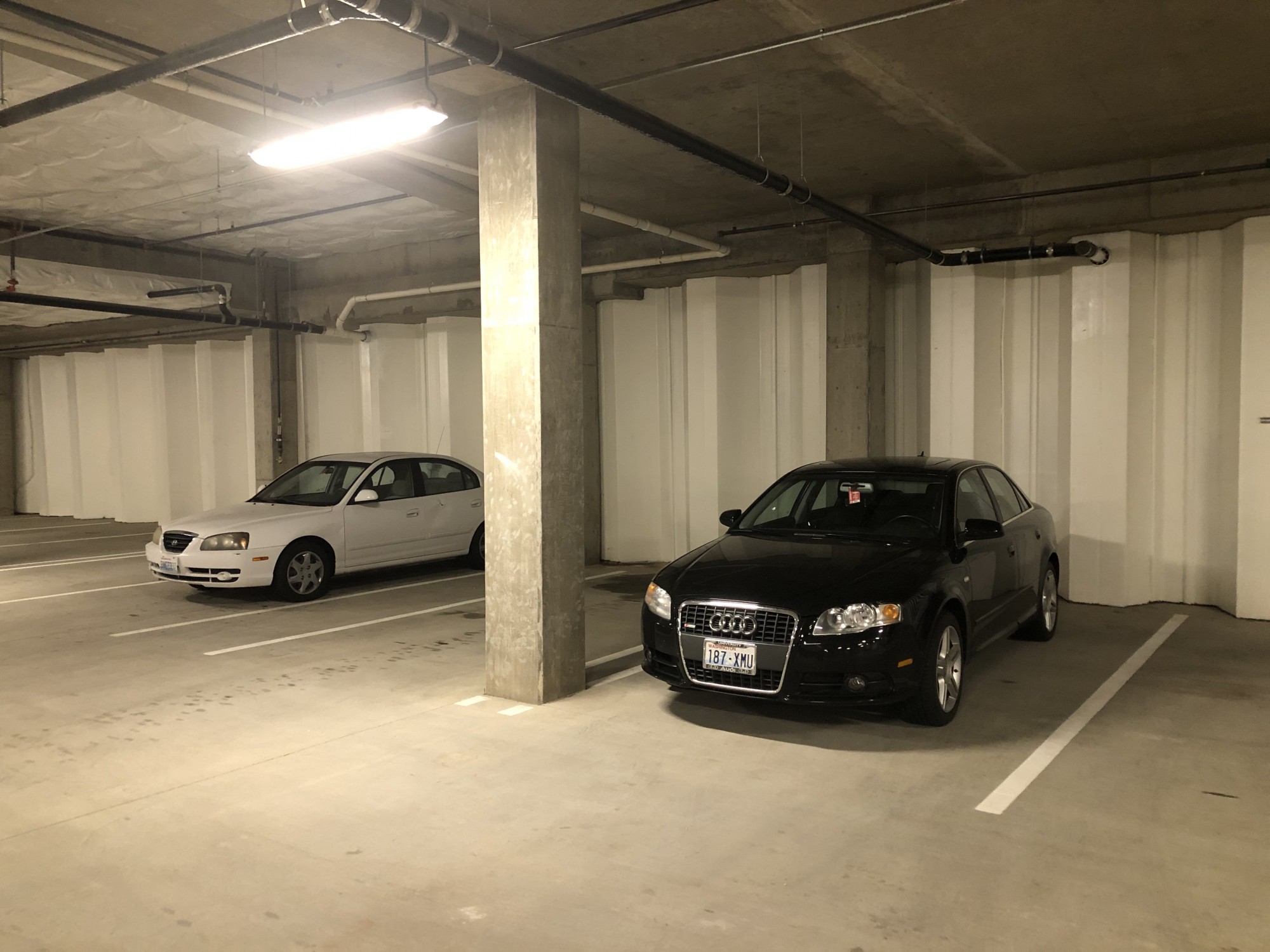
Going Down? Permanent Sheet Pile Foundations for Basement Structures
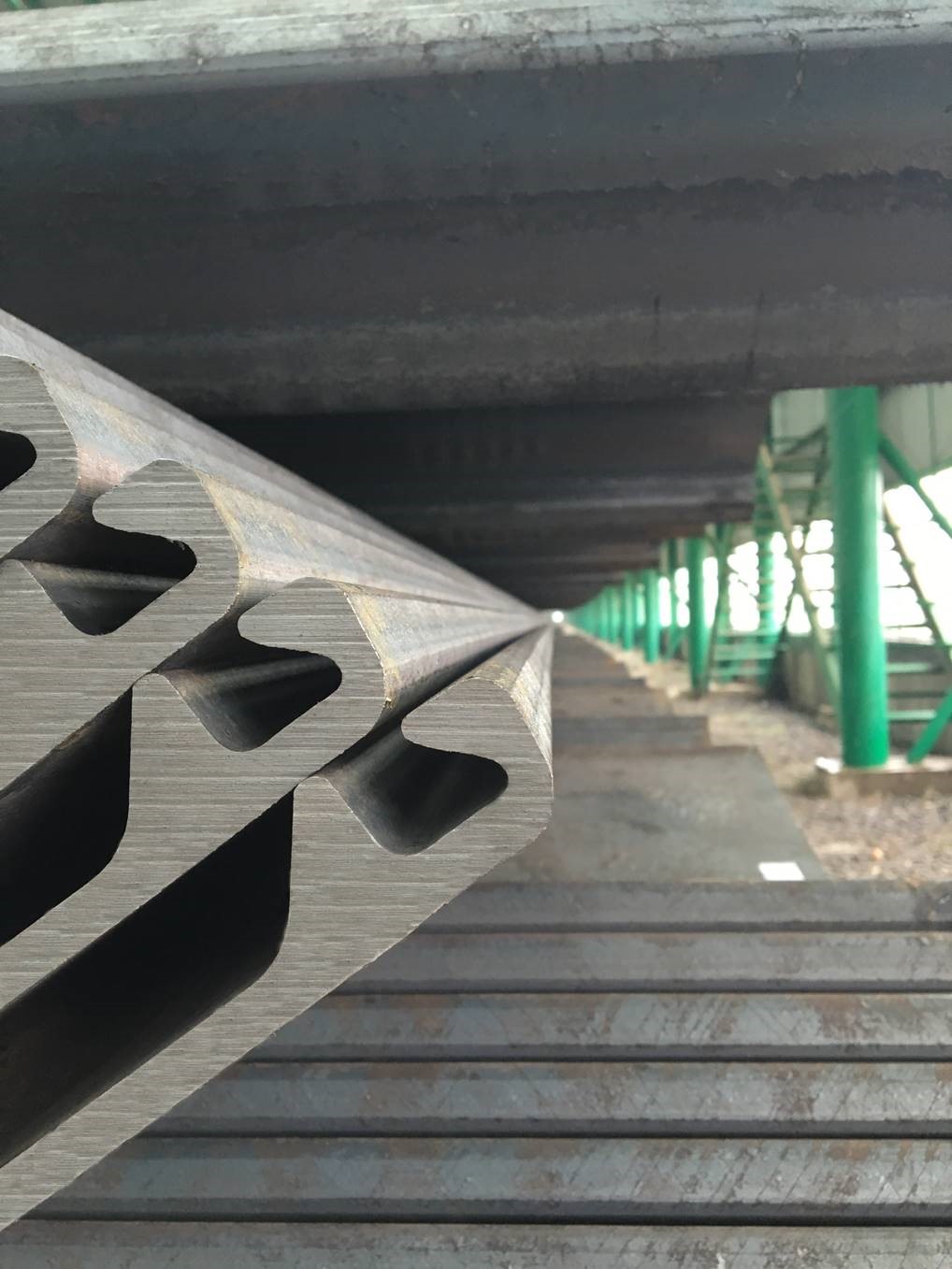
Sheet Piling 101
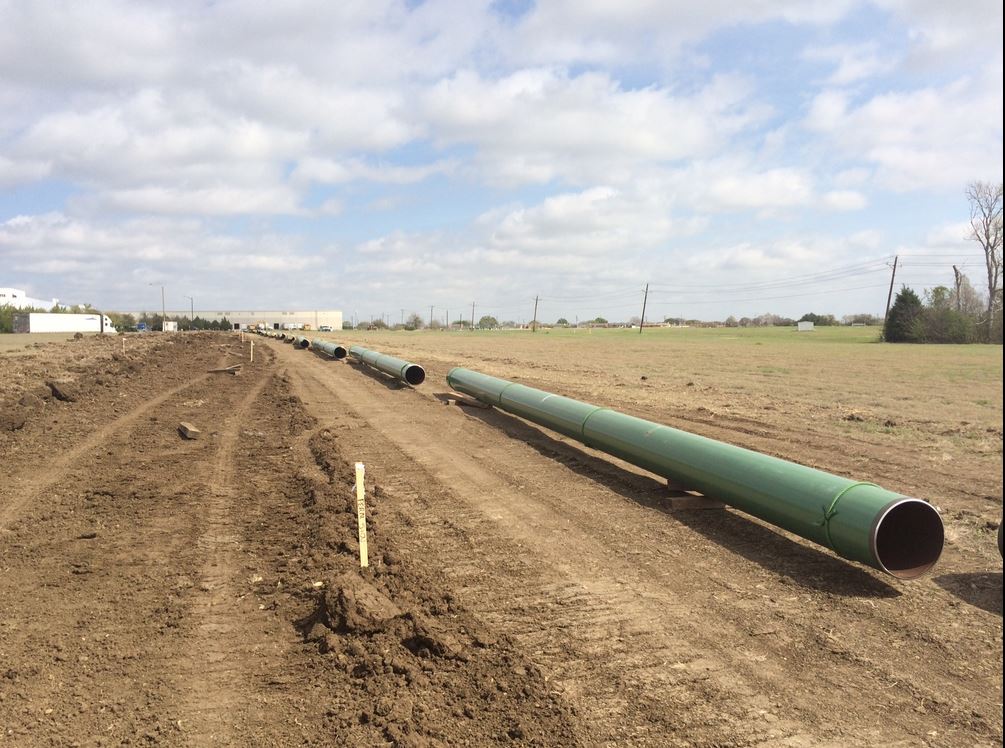
20-inch Lateral Relocation Pipeline News
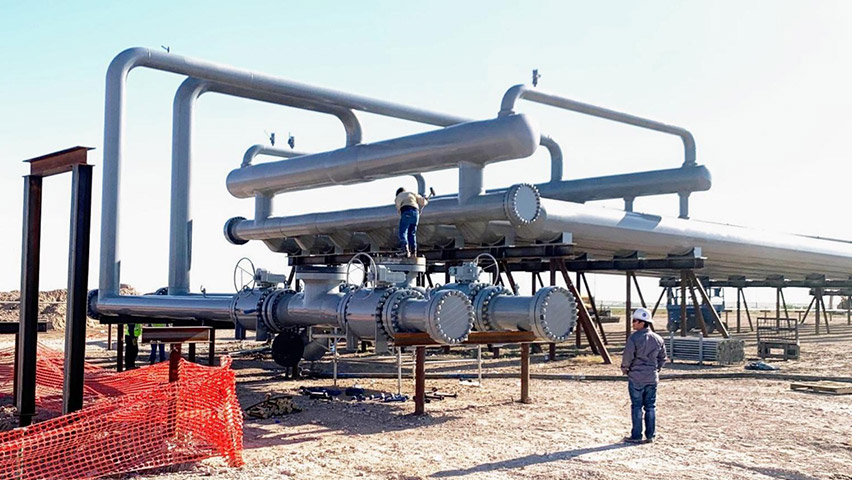
Benefits of Line Pipe
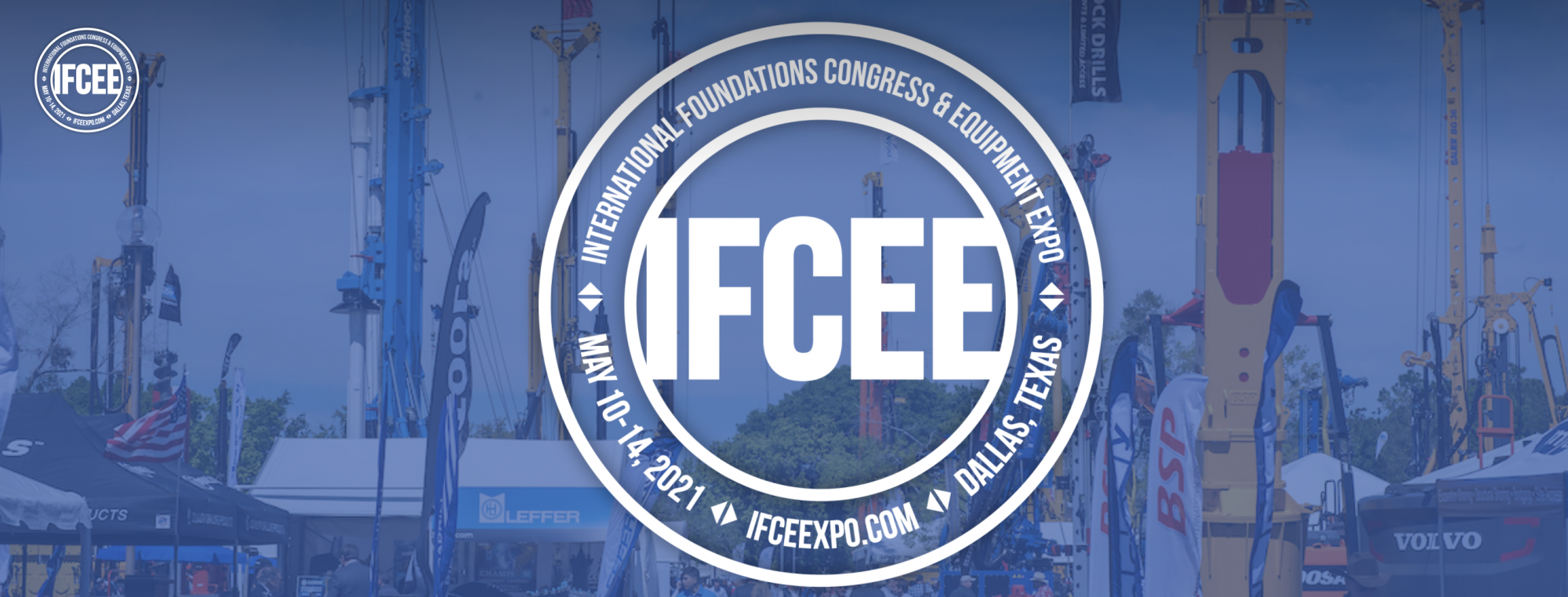
2021 IFCEE
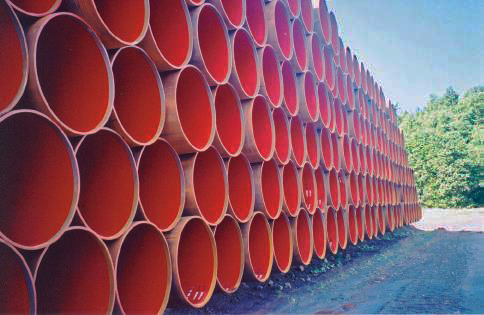