The Evolution of High-Frequency Welded Line Pipe
.jpg)
What is API Electric Resistance Welded (ERW) Line Pipe?
Electric Resistance Welded (ERW) pipe has been a widely used manufacturing method for decades, particularly in the oil & gas, infrastructure, and water transmission industries. This manufacturing process involves shaping a steel strip into a cylindrical form and using electrical resistance to generate heat, fusing the seam without filler material. However, early ERW technology—specifically low frequency (LF) AC welding—was prone to weld seam integrity issues, prompting significant industry advancements.
The Transition to High-Frequency Welding (HFW)
By the 1970s and 1980s, advancements in welding technology led to the widespread adoption of High Frequency Welding (HFW), an evolution of ERW that uses high-frequency currents (either induction or conduction) to heat and forge the seam under controlled pressure. Simultaneously, improvements in steel production—particularly the shift to fully killed steel, which removes oxygen and minimizes inclusions, enhanced weld quality, mechanical properties, and overall structural integrity. These advancements resulted in stronger, more uniform weld seams with improved toughness and fatigue resistance, eliminating impurities for a more reliable product. Given these improvements, all modern API 5L ERW pipe manufacturers now exclusively utilize high-frequency welding, prompting the industry to reclassify the product as HFW pipe.
Why HFW Replaced ERW in Industry Terminology
The outdated LF ERW process was associated with weld inconsistencies and failures, particularly in high stress applications such as offshore pipelines and high-pressure hydrocarbon transport. The transition to HFW terminology reflects improved weld integrity through high-frequency induction welding and compliance with modern industry standards, as API and regulatory bodies now recognize HFW as the benchmark for welded pipe.
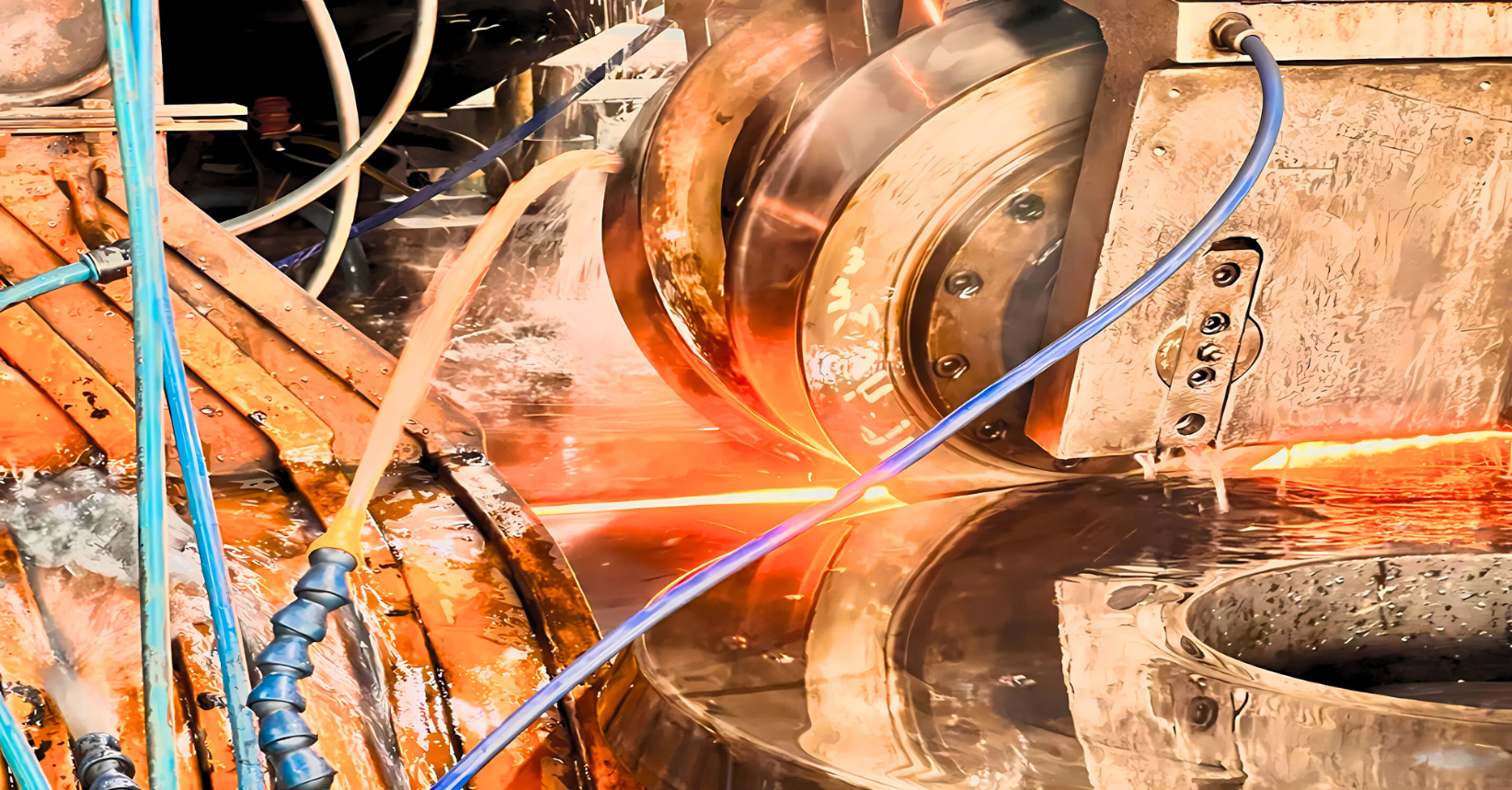
In the past, basic furnace annealing was used on some ERW pipes, but there was no precise control over the microstructure. Consequently, there were high defect rates due to grain growth and inconsistent mechanical properties, specifically in the weld area. Today, post-weld heat treatment uses induction annealing, controlling precise heat and targeting precise seam location. These controlled heating and cooling techniques drastically improve yield strength and ductility.
HFW pipe is now widely accepted and trusted for demanding applications, offering performance that rivals seamless pipe while providing cost and production efficiency advantages. While ERW remains a commonly used term, HFW has become the standard for high-frequency welded line pipe, distinguishing it from outdated, lower-quality ERW processes. That said, most in the industry still refer to it as ERW out of habit, even though modern manufacturing aligns with HFW technology.
Further Development of ERW Line Pipe: Quality & Offshore Acceptance
ERW line pipe has undergone significant transformation, overcoming historical material inconsistencies and weld seam concerns. Despite initial skepticism, improvements in steel production, welding precision, and rigorous testing have solidified ERW’s place in both onshore and offshore pipeline infrastructure.
By the 1970s, steel manufacturing had significantly improved, leading to cleaner and more predictable performance characteristics. One of the key breakthroughs was the transition to fully killed steel, a deoxidation process that removed oxygen and minimized inclusions. These advancements made ERW pipe viable for high-stress applications, including offshore environments. However, early concerns about fatigue resistance in harsh marine environments and weld seam reliability delayed widespread offshore adoption.
To counteract these doubts, U.S. pipe mills implemented stringent hydrostatic testing, which involved:
• Pressurization Beyond SMYS – Pipes were tested beyond 100% of Specified Minimum Yield Strength (SMYS) to ensure weld seam durability.
• Burst, Bend, and Flattening Tests – These tests confirmed mechanical integrity and weld toughness.
The Modern Standard: HFW Pipe’s Reliability and Industry Adoption
ERW line pipe has undergone a remarkable transformation from its early challenges to becoming a trusted solution for critical applications. The shift to cleaner, fully killed steel and improvements in welding technology have significantly enhanced its performance and reliability. While initial skepticism delayed its acceptance in offshore environments, the advancements in cleaner steel and technology in pipe mills have cemented ERW’s reputation as a strong, cost-effective, and dependable choice for modern pipeline systems.
MORE POSTS
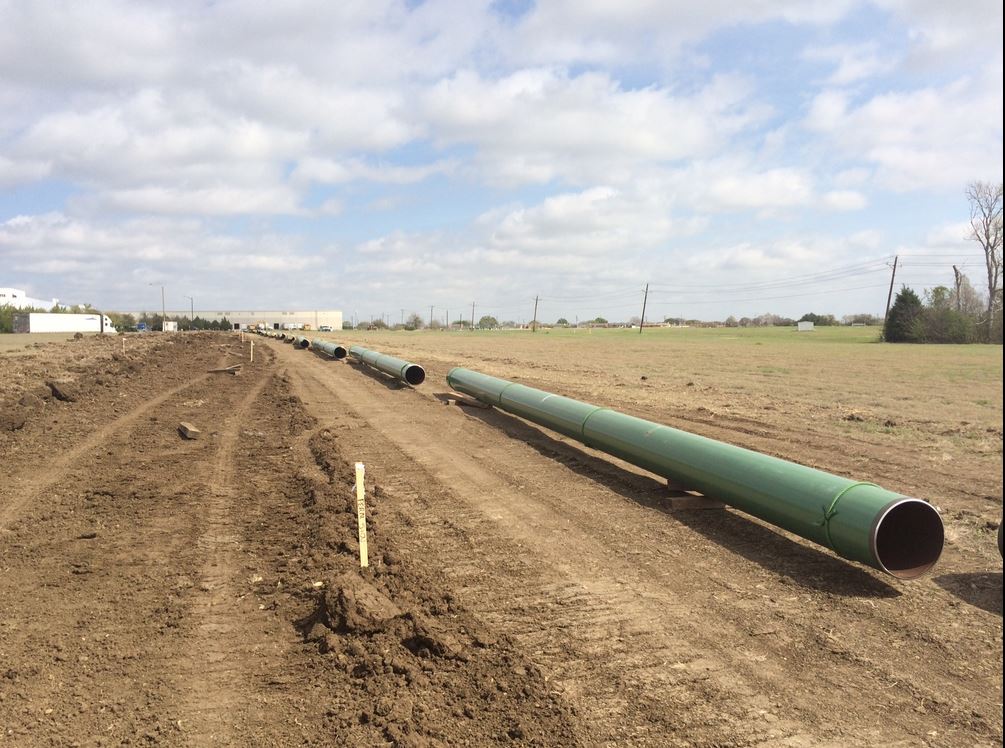
20 Inch Lateral Relocation Pipeline News
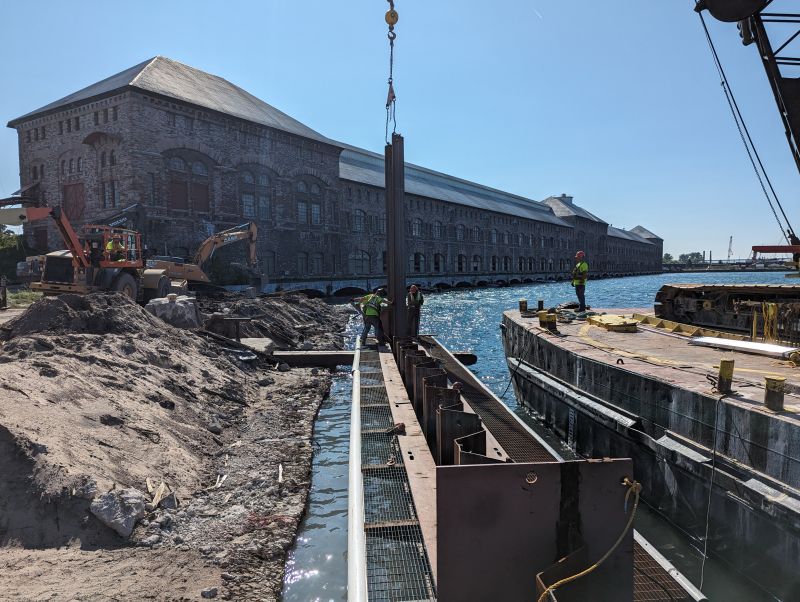
AZ Sheet Pile Project
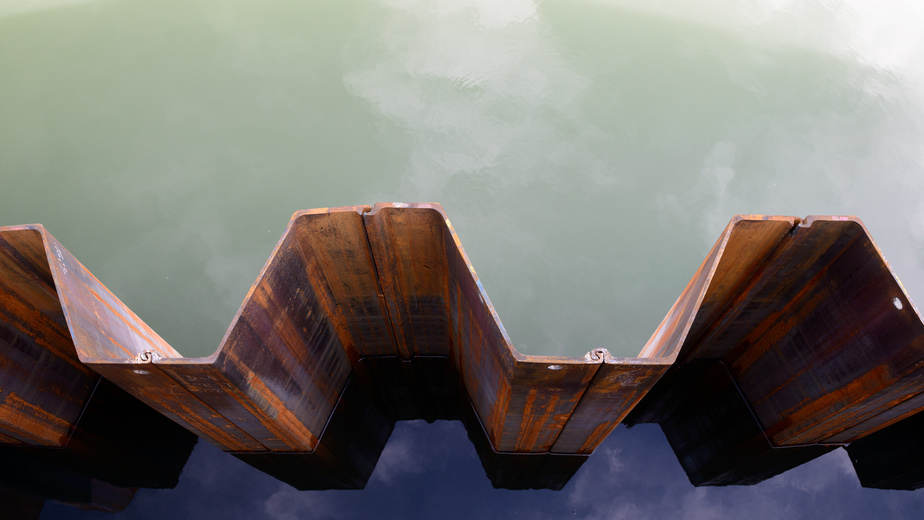
3 Common Uses for Sheet Piling
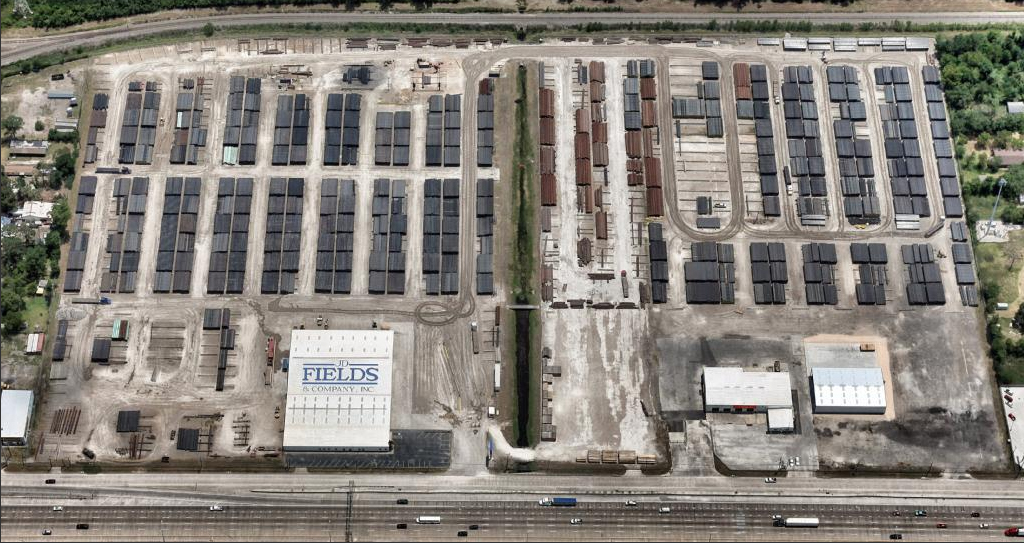
30,000 + Tons of Steel Pipe and Steel Piling Products
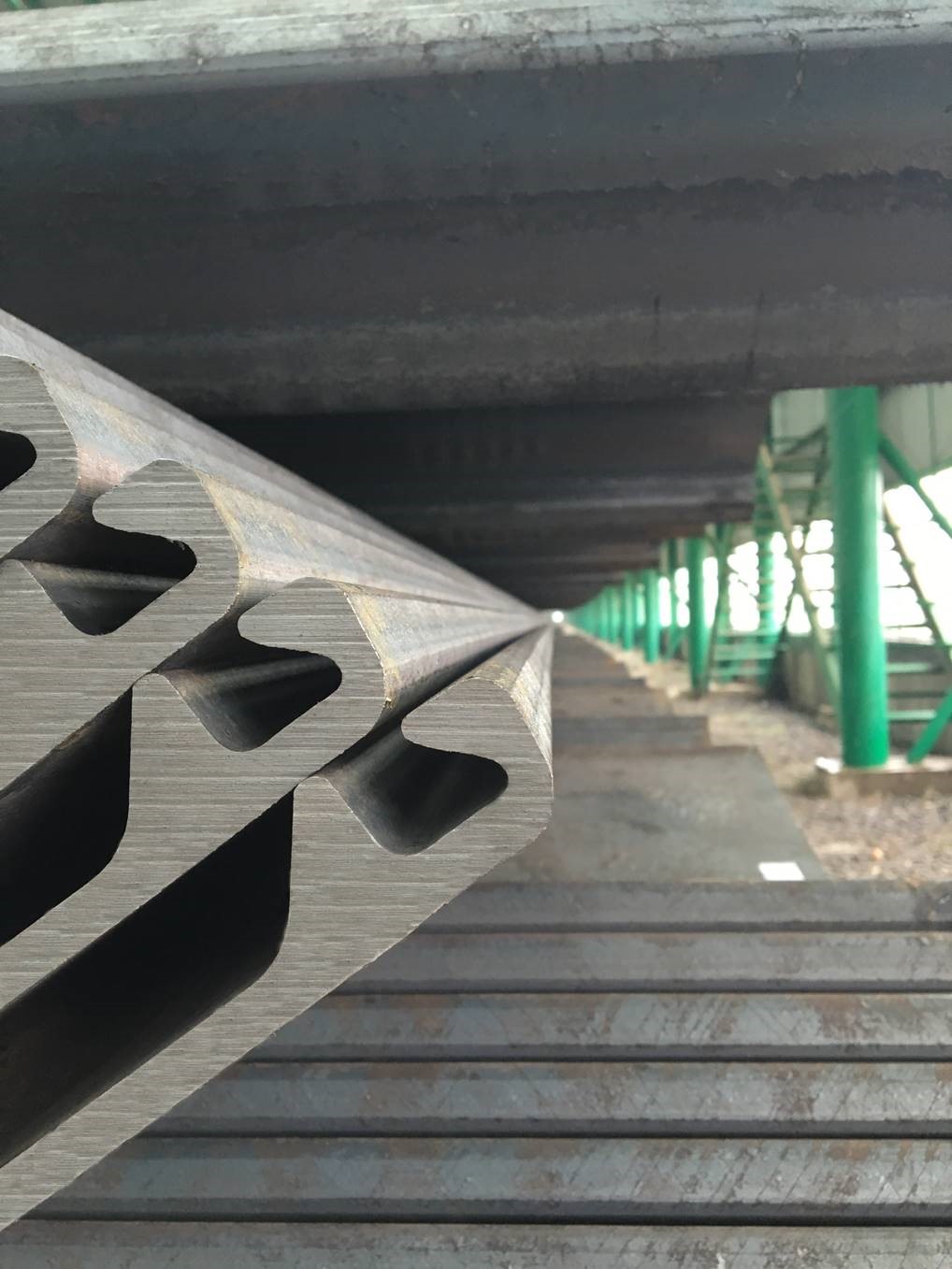
Sheet Piling 101
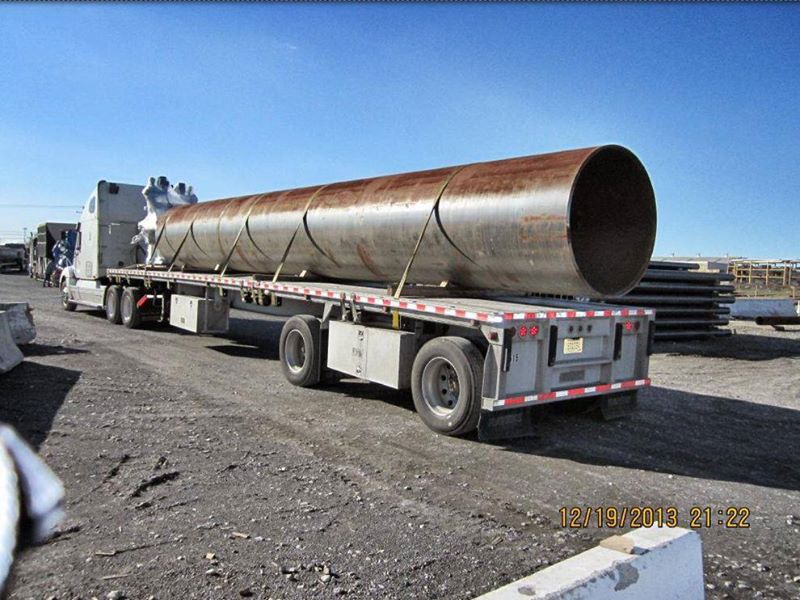
40 Foot Joints for the Atlantic Casino Resorts
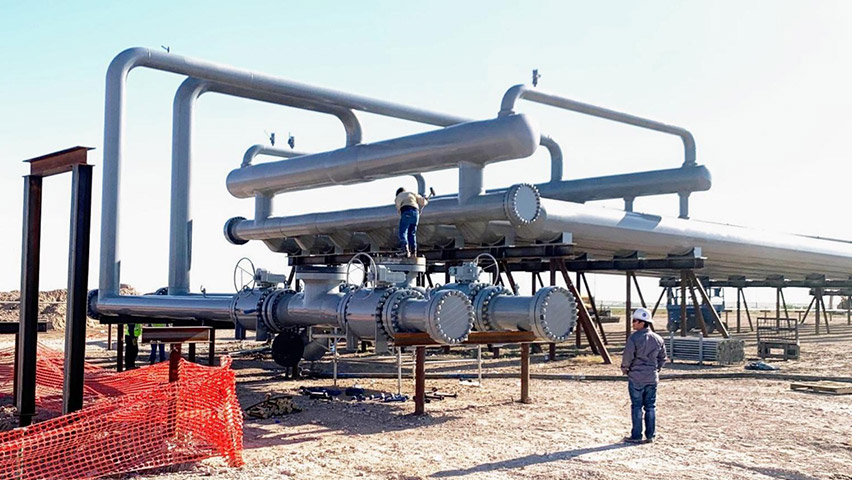
Benefits of Line Pipe
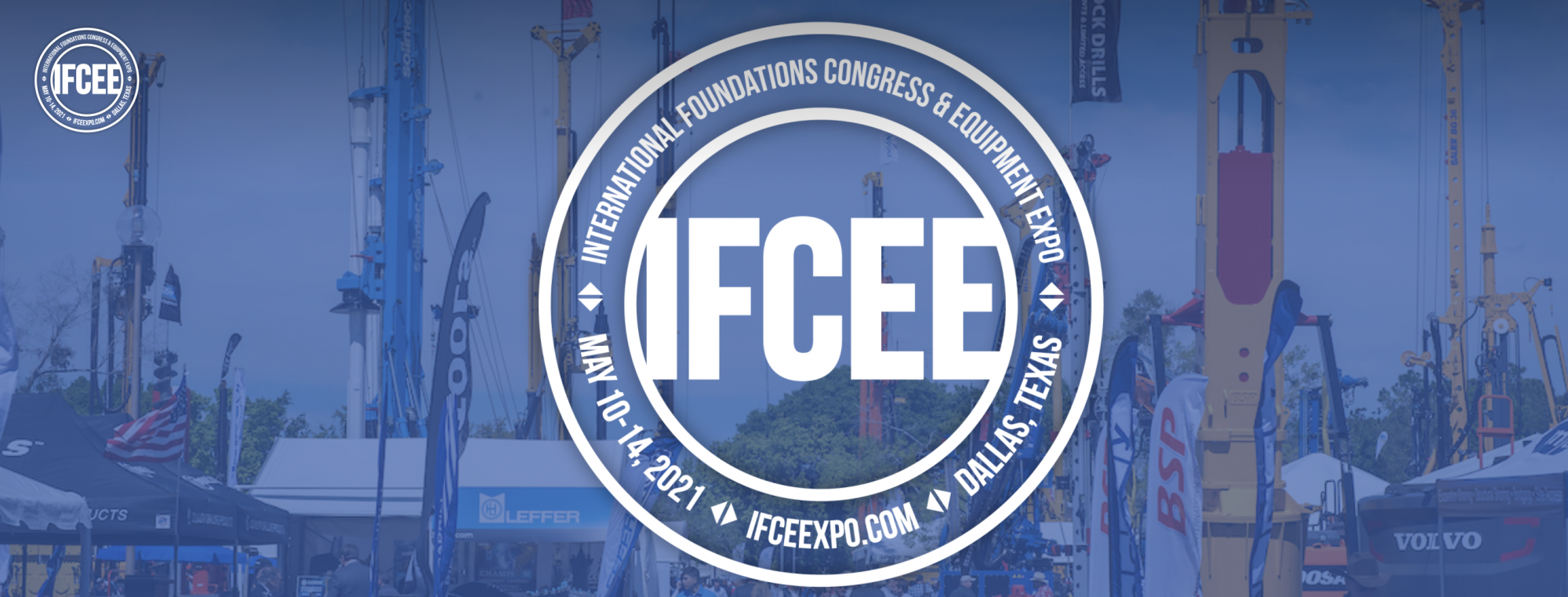
2021 IFCEE
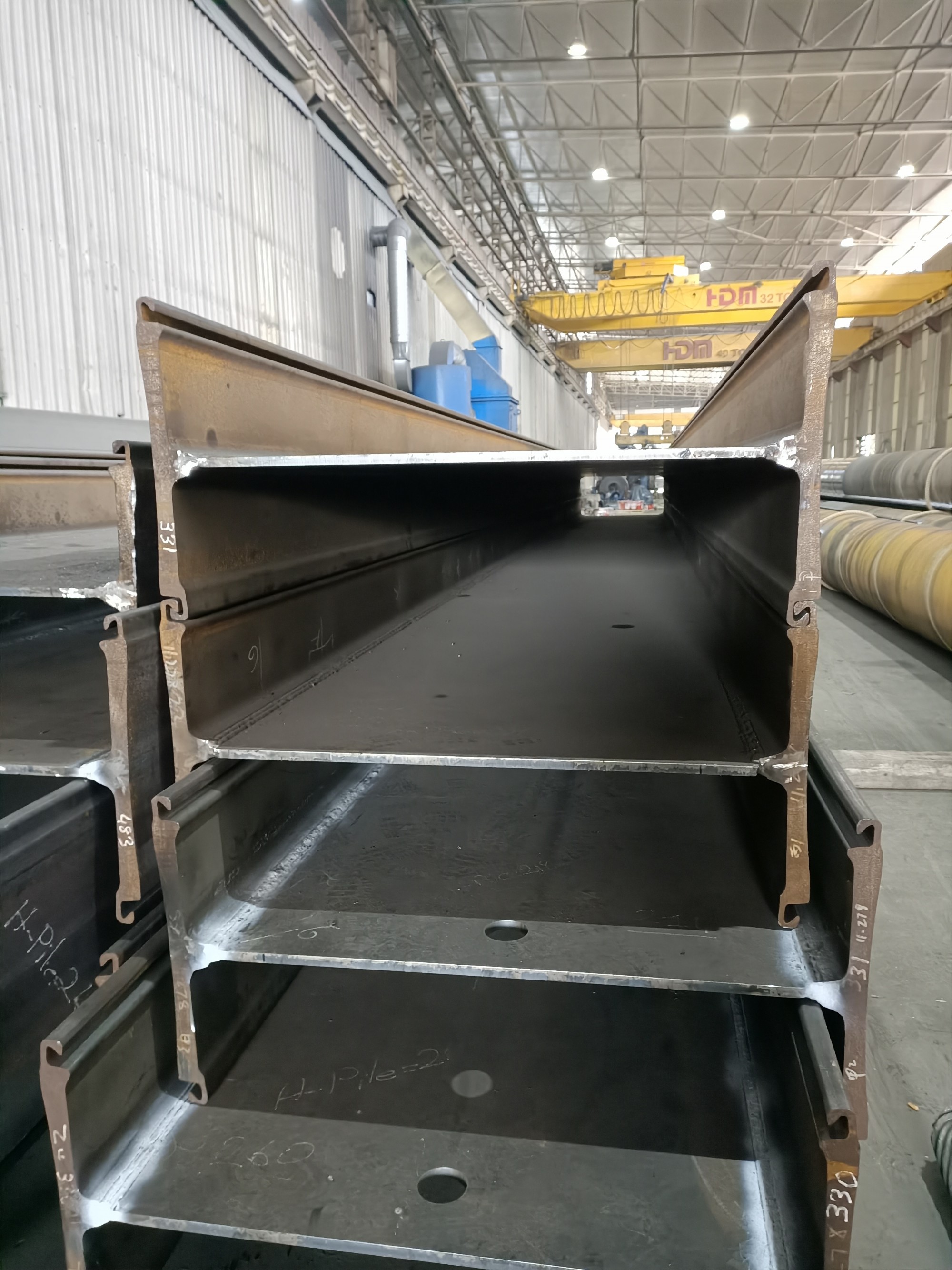
Evolution of Steel Piling Walls for Post Panamax Marine Structures
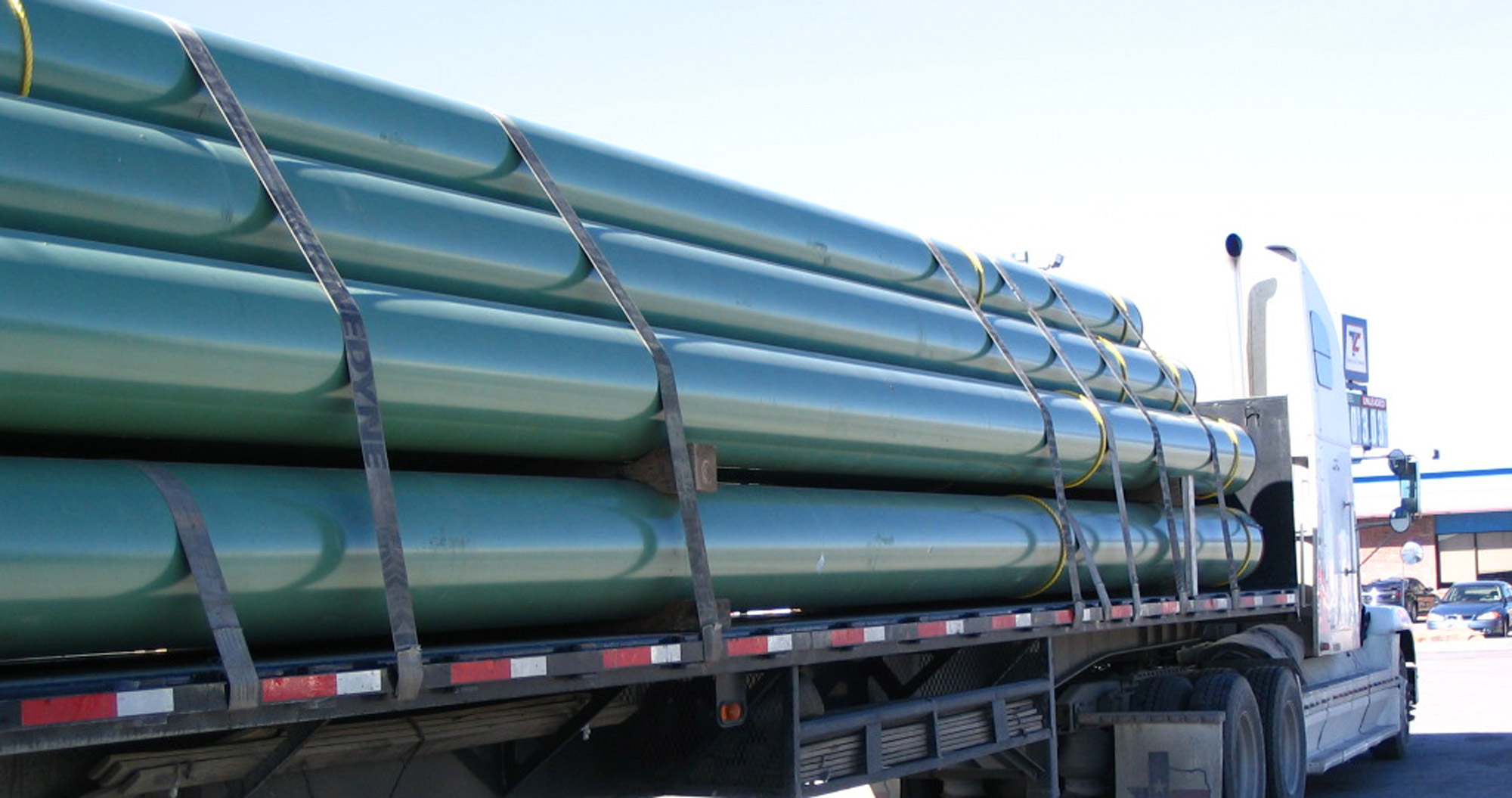
The Amazing Properties of Steel
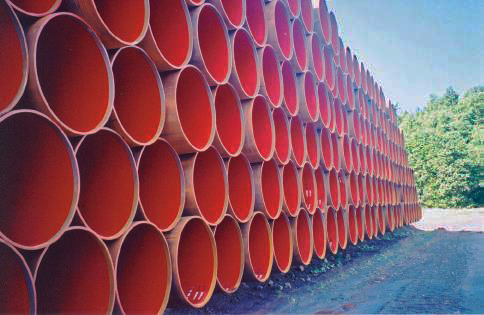
Coating Discussions Segment 1: Flowliner
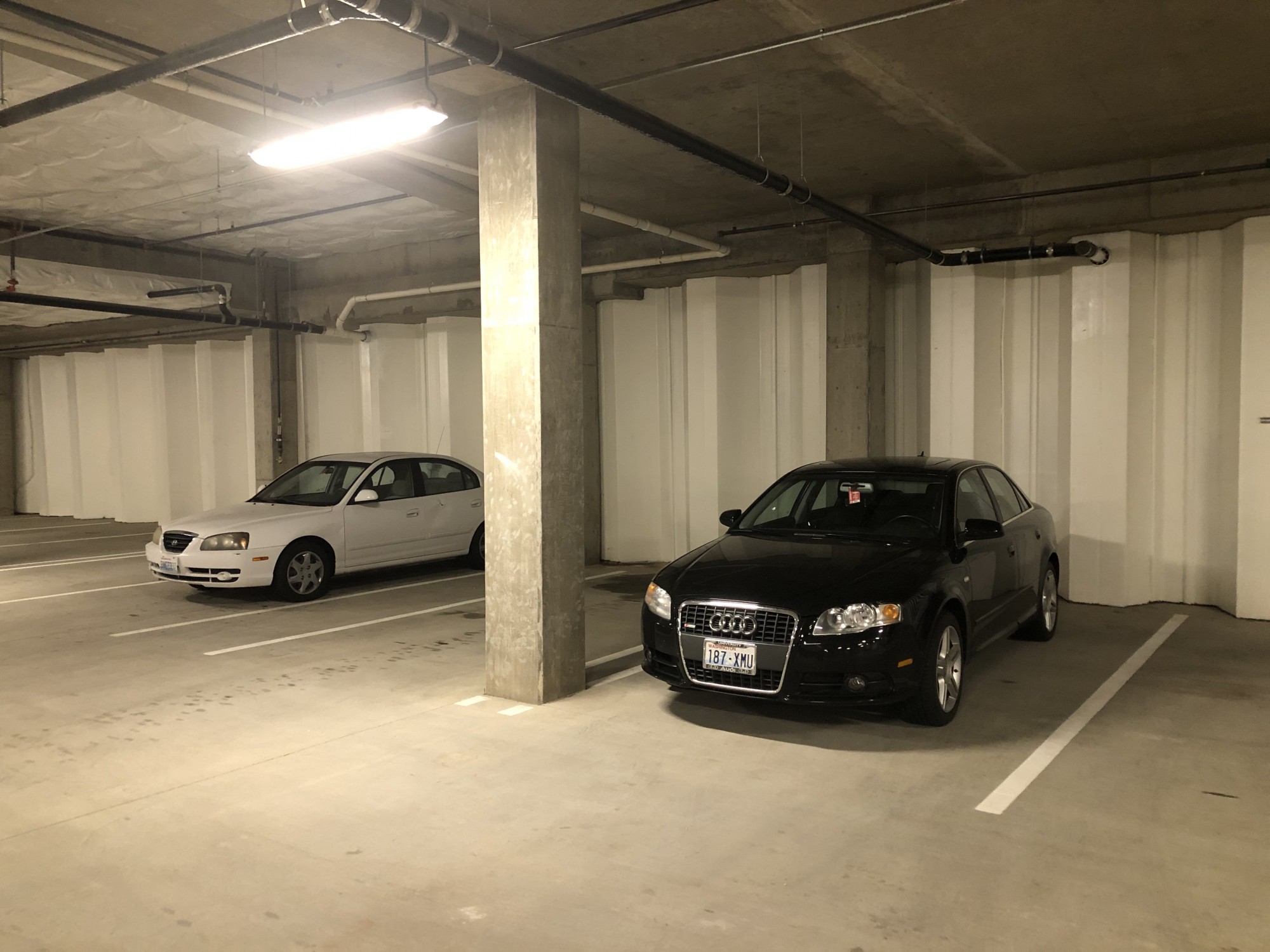